Custom plastic extrusion adapted to your industry needs
Custom plastic extrusion adapted to your industry needs
Blog Article
Secret Benefits and Factors To Consider of Applying Plastic Extrusion in Your Projects
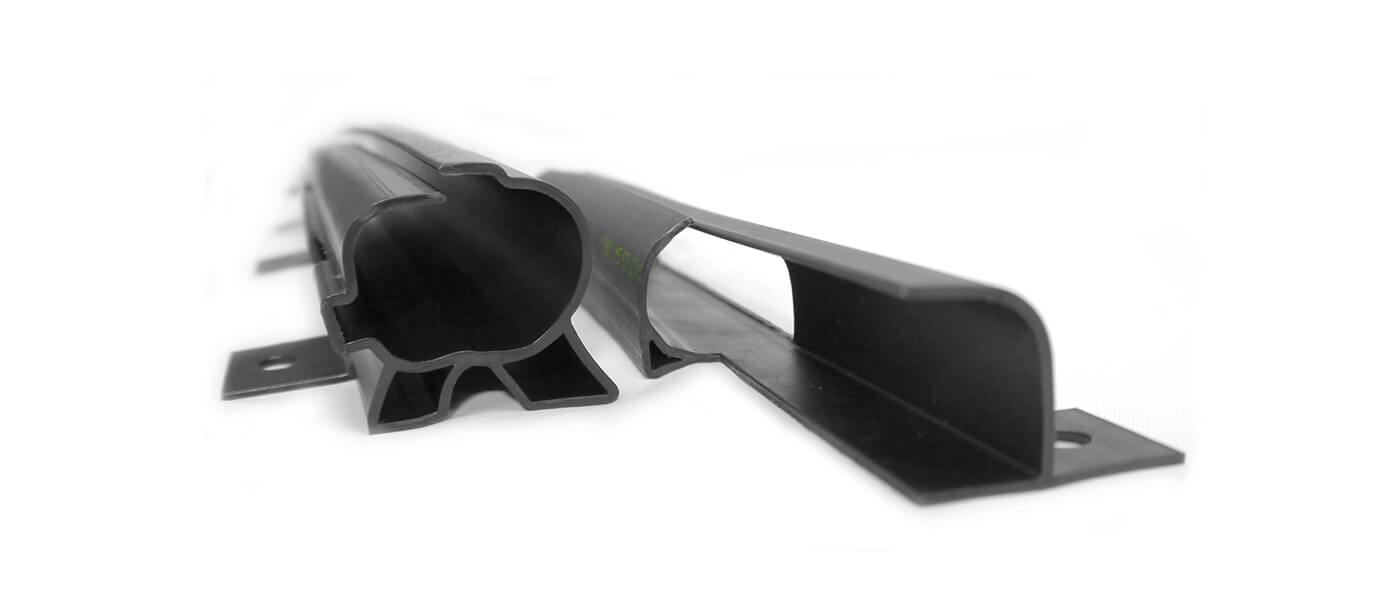
Recognizing the Essentials of Plastic Extrusion
Plastic extrusion, a staple in the production industry, is a process that entails melting raw plastic product and improving it into a constant profile. This profile, as soon as cooled down, can be cut into desired sizes or coiled for later use. The beauty of plastic extrusion lies in its flexibility. A large range of products, from piping to window structures, can be created. The process requires an extruder, a complex maker with a heated barrel, a rotating screw, and a die at the end. The plastic product, in the type of pellets, is fed into the extruder, where it's thawed and forced through the die, taking its form. The selection of plastic and the design of the die identify the item's attributes.
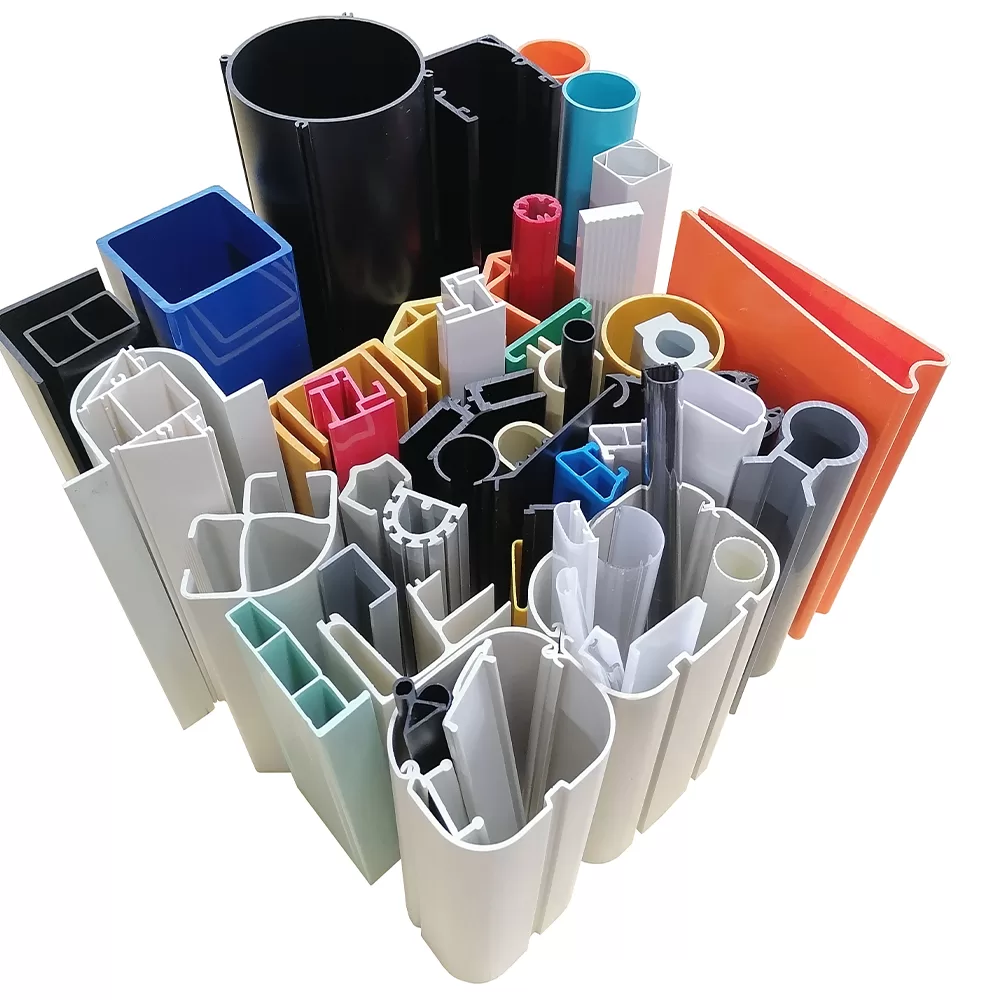
The Economic Advantage of Plastic Extrusion
The financial benefit of plastic extrusion lies primarily in two locations: affordable product production and valuable manufacturing rates. With plastic extrusion, organizations can generate high volumes of material at a reduced cost compared to various other approaches. The process boasts an excellent manufacturing speed, dramatically reducing time and further improving its financial viability.
Economical Product Manufacturing
A substantial benefit of plastic extrusion is its impressive cost-effectiveness. This manufacturing process enables constant, high-volume production with marginal waste, which equates right into reduced prices. The raw products used, usually plastic pellets, are fairly cost-effective contrasted to other compounds (plastic extrusion). The process itself requires much less power than lots of other production approaches, better decreasing expenses. Additionally, the extrusion process allows for a high level of precision fit the plastic, lowering the demand for expensive post-production changes or adjustments. Furthermore, the sturdiness and durability of extruded plastic products commonly imply much less need for substitutes, adding to long-term financial savings. All these factors make plastic extrusion a very cost-effective choice for numerous projects, supplying an appealing balance in between expense and performance.
Beneficial Manufacturing Speeds
While keeping the cost-effectiveness of the products, an additional significant benefit of plastic extrusion depends on its quick manufacturing speeds. This effectiveness in the production procedure is credited to the continual nature of the extrusion process, permitting for high-volume production in a reasonably brief time period. The rate of manufacturing directly associates to a decrease in labor expenses and an increase in outcome, therefore enhancing the total economic stability of the procedure. Additionally, the fast-paced production does not endanger the quality of the end product, making certain consistent and trusted results. This combination of speed, high quality, and cost-effectiveness emphasizes the substantial financial benefit of executing plastic extrusion in different projects.
Versatility and Modification: The Staminas of Plastic Extrusion
One of the prominent toughness of plastic extrusion depends on its flexibility and modification capacity. These high qualities unlock to unrestricted design possibilities, offering manufacturers the ability to customize items to specific requirements. This heightened degree of personalization not only boosts product functionality yet additionally significantly boosts product originality.
Endless Style Possibilities
Plastic extrusion beams in its capacity to use virtually infinite style possibilities. This method offers flexibility to create complex profiles and intricate forms, an accomplishment hard to attain with various other manufacture techniques. Owing to the liquid nature of liquified plastic, the procedure is adaptable sufficient to produce a varied series of measurements, sizes, and types. The plastic can be manipulated to match distinct requirements, permitting for the manufacturing of tailored geometries and conference particular client needs. Plastic extrusion can manage a selection of plastic types, increasing its application extent. This versatile strategy, for that reason, offers a large range of sectors from construction to automobile, packaging to electronics, and past. With plastic extrusion, the style opportunities are basically endless.
Boosting Item Individuality
The adaptability of plastic extrusion can considerably improve product individuality. This process permits designers to try out different shapes, sizes, and colors, providing the freedom to develop unique items that stand out on the market. It is this modification that offers a distinctive identity to each product, identifying it from its competitors.
In enhancement to its visual advantages, the customizability of plastic extrusion also offers useful benefits. Designers can modify visit this site the homes of the plastic according to the specific demands of the application, improving the product's functionality. They can make the plastic a lot more versatile, a lot more resilient, or much more immune to warmth, depending on what the item requires. Therefore, plastic extrusion not only improves product originality however additionally its energy and bankability.
Design Limitations in Plastic Extrusion: What You Need to Know
How can make constraints potentially impact the process of plastic extrusion? While plastic helpful site extrusion is flexible, layout restrictions can reduce its benefits. Certain complex layouts might not be practical due to the constraints of the extrusion procedure, potentially limiting the creation of detailed accounts. The procedure is much less appropriate for hollow or multi-chambered structures. Furthermore, the extrusion procedure may not always supply the desired surface area finish, particularly for those calling for high gloss or optical quality. Material choice can likewise posture challenges, as not all polymers appropriate for extrusion. High-temperature immune plastics, for example, might present difficulties. Understanding these restraints is essential for efficient application of plastic extrusion in your jobs. plastic extrusion.
Evaluating the Ecological Influence of Plastic Extrusion
While recognizing layout constraints is a substantial aspect of plastic extrusion, it is similarly crucial to consider its environmental ramifications. The process of plastic extrusion entails melting plastic products, possibly releasing damaging gases into the environment. Additionally, the resulting items are commonly non-biodegradable, adding to garbage dump waste. However, innovations in modern technology have actually enabled for more environmentally-friendly practices. For instance, using recycled plastic products in the extrusion procedure can decrease ecological effect. In addition, creating naturally degradable plastic alternatives can aid alleviate waste concerns. Reviewing these environmental factors is vital when executing plastic extrusion jobs, guaranteeing an equilibrium between performance, cost-effectiveness, and environmental duty.
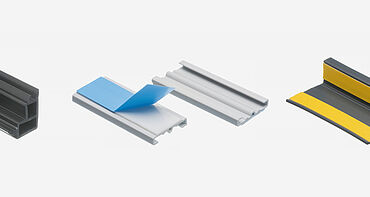
Case Research Study: Effective Projects Using Plastic Extrusion
Success tales in the field of plastic extrusion abound, showing both the flexibility and efficiency of this manufacturing procedure. plastic extrusion. One more successful instance is the production of plastic film for product packaging and farming. These instances highlight plastic extrusion's vital function in various sectors, proving to its versatility, cost-effectiveness, and dependable result.
Verdict
In final official website thought, plastic extrusion provides a effective and affordable technique for generating complex forms with very little waste. While it gives countless benefits such as cost-effectiveness and versatility, it's crucial to think about potential style limitations and ecological effects. Carrying out recycled or biodegradable materials can minimize these issues, improving sustainability. Including plastic extrusion into jobs can cause effective outcomes, as confirmed by countless case research studies.
Plastic extrusion, a staple in the production market, is a procedure that entails melting raw plastic product and improving it right into a continual profile. Plastic extrusion can deal with a range of plastic types, broadening its application range.Just how can design limitations possibly affect the procedure of plastic extrusion? The process of plastic extrusion includes melting plastic materials, potentially releasing dangerous gases into the atmosphere. Making use of recycled plastic products in the extrusion process can minimize environmental impact.
Report this page